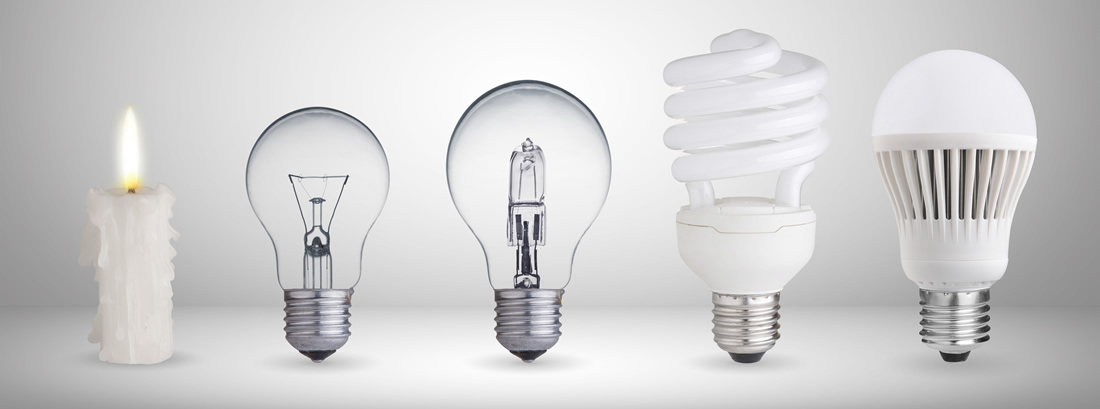
Beispiele für energetische Optimierung
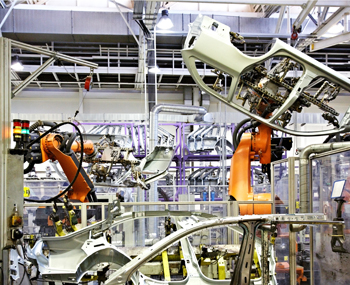
Energieeffizienzberatung für einen Automobilhersteller
→ IST-Situation: Der Karosserierohbau eines Automobilherstellers hat einen hohen Energieverbrauch und soll im Rahmen der DIN ISO 50001 untersucht werden.
→ Ergebnis: Durch eine energieeffiziente Neu-Programmierung der Steuerung und Abstimmung der Prozesse wurde der Stromverbrauch um ca. 30% reduziert.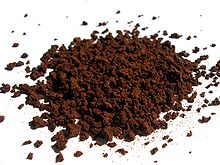
Energieeffiziente Herstellung von Pulverkaffee
→ IST-Situation: Die heiße Abluft aus der Sprühtrocknungsanlage entweicht ungenutzt an die Umgebung mit der Aufgabe die Abwärme aus der Abluft nutzbar zu machen.
→ Ergebnis: Durch den Umbau der Trocknungsanlage kann der Gasverbrauch um ca. 25% reduziert werden.
Energieeffizienzberatung für einen Zoofachmarkt
→ IST-Situation: Ein Zoofachmarkt hat einen sehr hohen Energieverbrauch in der Lüftungsanlage und somit hohe Energiekosten.
→ Ergebnis: Reduzierung der Energiekosten für die RLT über 40%. Durch die Anpassung und Optimierung der raumlufttechnischen Anlage wurden die Energiekosten des Unternehmens um ca. 60.000 € gesenkt.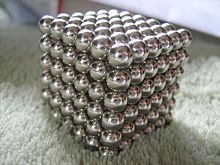
Energieeffizienzberatung für einen Permanent-Magnethersteller
→ IST-Situation: Insgesamt war der Betrieb schon in Teilbereichen optimiert, z.B. wurde bereits ein BHKW mit einer Absorptionskältemaschine eingesetzt. Es zeigte sich aber, dass durch konsequente Umstellung der Beleuchtung auf LED-Leuchten ein großes Einsparpotential erschlossen wurde.
→ Ergebnis: Wir haben nachgewiesen, dass durch die Erneuerung der Beleuchtung eine jährliche Einsparung von 180.000 € erzielt wird. Über die gesamte Betriebsdauer (ca. 10 Jahre) können über 1,5 Mill € eingespart werden. Die Investition amortisiert sich nach 2 Jahren.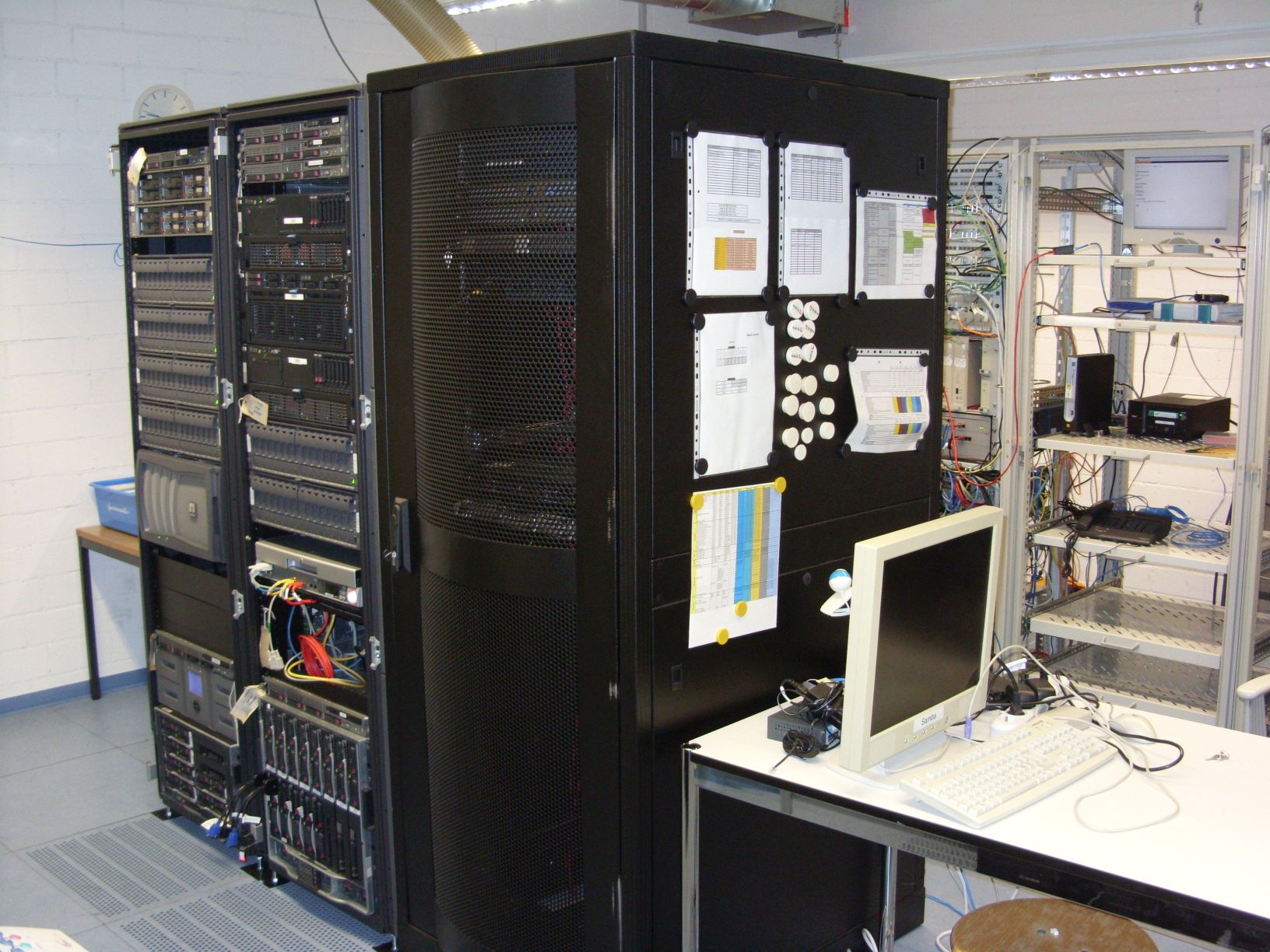
Optimierung eines Firmenrechenzentrums
→ IST-Situation: Für den Betrieb des Rechenzentrums werden pro Jahr ca. 350 MWh Strom benötigt, das verursacht Kosten in Höhe von ca. 45.000 €.
→ Ergebnis: Bei Umsetzung aller Maßnahmen können bis zu 30% der Stromkosten eingespart werden.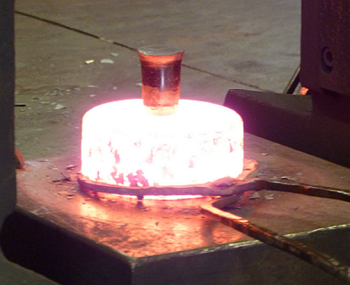
Energieeffizienzberatung für eine Hammerschmiede
→ IST-Situation: Die Hammerschmiede hat sehr hohe Energiekosten aufgrund der alten ölbetriebenen Schmiedeöfen. In den Schmiedeöfen werden die Werkstücke auf ca. 1200°C erhitzt bei jährlichen Betriebszeiten
von ca. 3000 Stunden. Die Abwärme aus den Öfen wird bisher nicht genutzt.